myRGA Residual Gas Analyzer
Reliable and Cost Effective Gas Analysis. The LINXON myRGA provides simple, easy and affordable gas analysis.
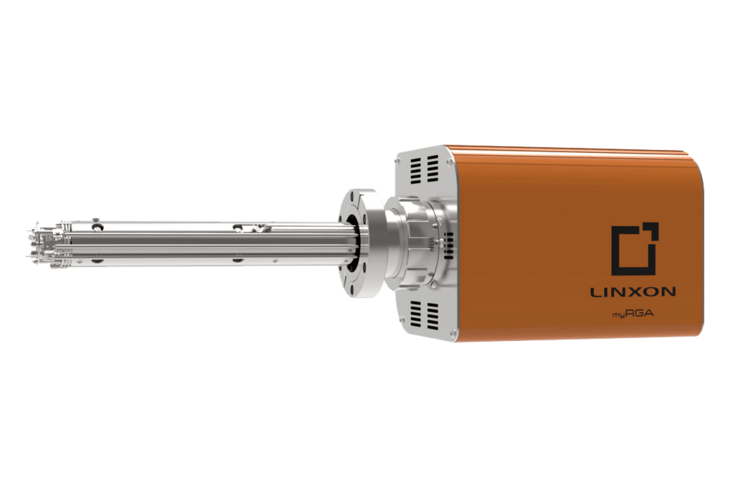
LINXON myRGA Residual Gas Analyzer
LINXON myRGA is a dependable residual gas analyzer (RGA) with the performance and price you need for gas analysis, air leak detection and contamination detection. This simple to use RGA is designed for self-sufficient customers with simple software, an online knowledge base, and do-it-yourself maintenance.
- Low price gas analyzer for air leak detection and process monitoring at an exceptional value
- Straightforward operation: simple initial set-up due to intuitive software
- Minimal maintenance and easy, field replaceable filament and ion source assemblies, and electron multiplier
- Simple integration options anyone can learn due to http interface and LabVIEW development kit
- Always in stock for fast delivery
Check out our FAQs for more infomation.
FAQ
Useful answers all around your myRGA
What is important for the installation of the RGA?
Follow the instructions provided in the operating manual. See the section titled, “Hardware Installation.” Read the instructions carefully before installation, and beware of all cautions and warnings. Do not touch any surface on the vacuum side of the sensor with bare fingers.
Where can I find the LINXON myRGA Operating Manual?
At the onboard web server, and at linxon.net
Where can I find the API documentation?
The API documentation can be downloaded here.
Where can I download the LabVIEW driver?
linxon.net. Instructions are included.
How do I start the first measurement?
Refer to the section of the operating manual titled, “Connecting to the Onboard Web Server.” This will bring up the onboard web browser. From there you can navigate to the Monitor screen where you can run an analog scan. Verify the chamber pressure is <5E-04 Torr before turning on emission and running a scan. Ensure emission is on during the scan.
Where can I find a 3D model of the RGA?
linxon.net
How do I get LabVIEW to recognize my RGA?
See the LabVIEW instructions that are included with the LabVIEW drivers. Set the “LINXON IP Address” at the beginning of the block diagram before running an Example.
What are the computer requirements for the onboard web server?
Refer to the section of the operating manual titled, “System Requirements.”
What does it mean when my RGA suddenly reports nothing but negative values or near zero values?
Emission is likely not on. Turn on emission. If you are unable to turn on emission, perhaps the filament is blown or overly contaminated. See the operating manual for instructions on how to determine if a filament kit replacement is required.
How do I get the data from two RGAs to match?
Calibrate Sensitivity and EM on both RGAs. Calibrate to the same mass and the same target, while under the same chamber conditions. This practice is referred to as “chamber matching.”
How do I reduce the amount of water in the background?
Bakeout the sensor until the water signal has flat-lined. If water continues to be an issue, verify there are no air leaks in the sample environment. Note that the maximum baking temperature is 300degC with the sensor switched off and the electronics removed. During operation, the temperature should not exceed 150 degC if the EM is on, or 200 degC if the EM is off.
How do I address a “cold-start” error?
“Warm-start” and “cold-start” errors typically mean the filament has blown. Review the historical data that took place prior to the error. First, verify that the pressure was < 5E-04 Torr throughout the scan, then observe the mass trends. A gradual loss of sensitivity (gradual weakening of signals) indicates that the filament has blown as a result of contamination build up. A sudden loss of sensitivity (a sudden drop in signals) means the filament was probably subjected to a pressure burst. More information about warm-start and cold-start errors can be found in the Symptom-Cause-Remedy Chart located in the operating manual.
How often should I tune and calibrate?
This is different for every case. Take a fingerprint scan after tuning and calibrating. In two weeks or so, recreate the same circumstances in your chamber. Flow the same gases and bring the chamber to the same pressure as when you last tuned and calibrated. If the intensity of the signals for each controlled gas is still the same as it was when you tuned and calibrated, there is no need to tune and calibrate. Instead, repeat this in another two weeks. Repeat until you witness a drop in signal strength. Once you witness a drop in signal strength, tune and calibrate. You have now established your tune and calibration cycle time.
What can cause the RGA to prompt a “Hardware warning: anode potential,” or “Hardware warning: focus potential” alarm?
Contamination may have shorted the anode plate or the focus plate to neighboring hardware. Bakeout for several hours in an effort to break the contamination free, or gently spray the ion source with an inert gas to try and dislodge the contamination. If this is unsuccessful, replace the ion source.
Our process pressure is at or near the RGA’s maximum operating pressure. How accurate is the RGA at or near maximum operating pressure?
Optimal sensitivity is achieved at 1E-05 Torr or lower. However, you can still expect a sensitivity of approximately 5E-05 A/Torr when sampling near the instrument’s maximum operating pressure, depending on process conditions. Sampling at or near the instrument’s maximum operating pressure is not a concern unless the process is vulnerable to pressure bursts, in which case it is recommended that you take measures to protect the filament from pressure bursts.
What should we change after a filament failure?
Review the historical data that took place prior to the error. A gradual loss of sensitivity indicates that the filament has blown as a result of contamination build up. If contamination is suspected, neighboring hardware is likely contaminated as well, so it is recommended that you replace the entire ion source. A sudden loss of sensitivity, on the other hand, means the filament was probably subjected to a pressure burst. In that case, it is only necessary to replace the filament assembly.
Can I extend the lifetime of the filament by shutting it off when the RGA is not used?
Leaving the filament off when not in use is good practice to extend the lifetime of the filament. However, there are two things to consider. Beware that frequent toggling on and off of the emission puts a strain on the filament. Additionally, some processes tend to coat cold spots, so if you have that type of process, you may benefit from leaving the filament on at all times to keep the ion source clean.
Is the RGA equally as sensitive to all masses (m/z)?
As m/z increases, the magnitude of RF and DC applied to the quadrupole increases to achieve those pass bands. As the magnitude of RF and DC increases, transmission factor decreases. See the section of the operating manual titled, “Glossary,” for an explanation of transmission factor. This effect can cause signals with a weak intensity to be lost in the background noise. To ensure this is not taking place, increase the electron multiplier gain to improve signal-to-noise ratio.
What is the ideal pressure for RGA calibration?
Ideally, total pressure should be anywhere from 1E-06 Torr to 1E-05 Torr during calibration. Consistency is key. For instance, if you calibrated at 1E-05 Torr last time, you should calibrate at 1E-05 Torr in the future as well.
Which is better, calibrating to one gas or to a gas mixture?
Calibrating to one specific mass is the preferred method for calibrating sensitivity. Tuning, on the other hand, requires a gas mixture.
Can the RGA be damaged by certain gases?
Two filament materials are offered, tungsten and yttria-coated iridium. For oxygen and water rich applications, yttria-coated iridium should be used. For halogen rich applications, a tungsten filament should be used.
What is the difference between dwell time and acquisition time?
Dwell time is the amount of time spent acquiring each data point. Note, a single AMU can consist of multiple data points. For instance, if you collect 5 points per AMU at a dwell of 2 milliseconds, you will spend 10 milliseconds on each individual AMU. Dwell time and points per AMU are user configurable. “Acquisition time” is not LINXON terminology, but it refers to the total time the RGA was collecting data.
What is the default dwell time?
32 ms
What is noise and what is the nominal noise level of a 100 and a 200 AMU system?
Noise is the standard deviation of the collected signals, plus electrical noise from RGA hardware. There is inherent background noise in every RGA, which varies from system to system. The more masses collected and the larger the m/z collected, the greater the noise. The greater the total pressure, the greater the noise. Lastly, you can expect more noise when the EM is on, as opposed to scanning with FC only.
How long should we let the filament warm up before starting data acquisition?
You can start data acquisition immediately, with little to no impact to the data. However, for particularly critical measurements, and when tuning or calibrating, allow the filament to warm up for 15 minutes.
How long should we let the filament cool down before venting the chamber?
This is not a concern. As long as emission is off before the chamber pressure is > 5E-04 Torr, there is no risk to the filament.
Can we bake the RGA with the electronics box attached?
See the section of the operating manual titled, “Bakeout of Quadrupole.”
What is the operating temperature range for the RGA electronics box?
5 to 50 degC
Which should I use, “selected mass” mode or “spectrum” mode?
There are a number of benefits to each mode. For instance, if you don’t yet know the chemical makeup of the gases in your sample environment, you would likely use “mass spectrum” mode to identify all the masses that are present. On the other hand, if you already know what gases are present in your chamber, but you are only interested in a select few gases, you should use “selected mass” to monitor only the masses of interest.
How should we handle the sensor when installing or de-installing?
Please refer to the section of the operating manual titled, “Sensor Installation.” Pay close attention to the cautions and warnings listed in that section.
If we have multiple RGAs, how should we assign IP address for each RGA?
Please see the section of the operating manual titled, “Installing Multiple Sensors.”
When do we need to calibrate the RGA total pressure?
If you are just monitoring data in units of raw current, routine total pressure calibrations are not necessary. On the other hand, if total pressure is used as a variable in calculations (either in the onboard web server, in LabVIEW, or offline), it is wise to calibrate total pressure as often as you tune and calibrate sensitivity and EM. Beware that sensitivity equals A/Torr, where Torr equals the total pressure as measured by the total pressure plate. Therefore, because sensitivity is used to calculate partial pressure and to convert to parts per million (ppm), it is wise to calibrate total pressure on a regular basis if you are analyzing data in partial pressure mode or in units of ppm.